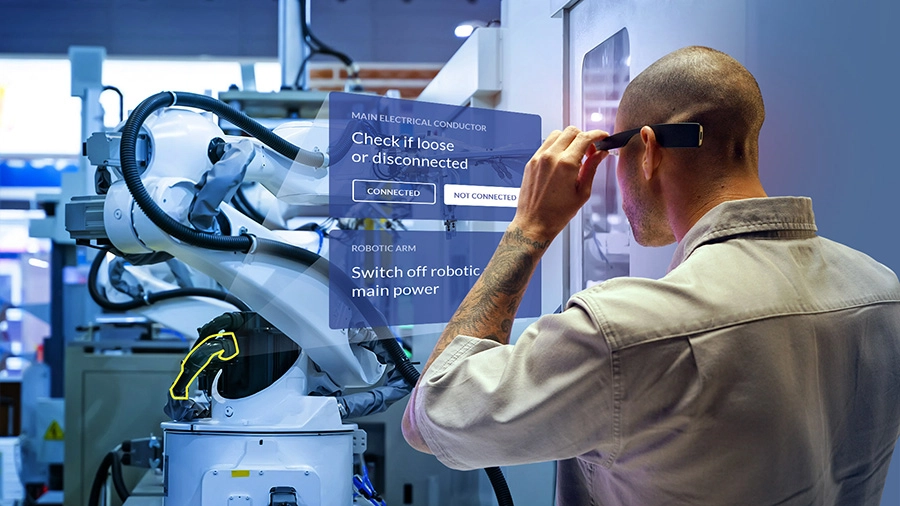
CareAR for Manufacturing
Manufacturers not only have to support the products that they deliver but also the increasingly complex systems that create those products. Making expertise accessible with live visual AR interactions, instructions, and intelligence can drive game-changing business outcomes that deliver significant operational efficiencies, reduce cost, and create improved customer and employee experiences.
CareAR for Manufacturing
Manufacturers not only have to support the products that they deliver but also the increasingly complex systems that create those products. Making expertise accessible with live visual AR interactions, instructions, and intelligence can drive game-changing business outcomes that deliver significant operational efficiencies, reduce cost, and create improved customer and employee experiences.
CareAR for Manufacturing
Manufacturers not only have to support the products that they deliver but also the increasingly complex systems that create those products. Making expertise accessible with live visual AR interactions, instructions, and intelligence can drive game-changing business outcomes that deliver significant operational efficiencies, reduce cost, and create improved customer and employee experiences.
Industry Challenge
Improve Uptime, First Time Resolution, and Carbon Footprint with AR
Disruptions and risks are not unfamiliar to manufacturing leaders who have been facing recurring supply chain disruptions, labor shortages, and a widening skills gap. These, combined with equipment downtime, slow resolution of issues, speed of business processes, and smart factory initiatives, have left companies racing to drive efficiency and operational excellence.
Top Challenges in Manufacturing Industry
Costly downtime due to machine malfunctions and long handling time
First time resolution of issues for customers and technicians
Skill curation and knowledge capture; talent retention and workforce stability
%
of software CTOs expect immersive technologies to be focused on assembly errors.
Improve First Time Fix Rates
Visual expert guidance speeds resolution and boosts uptime, minimizing disruption to the business and saves everyone time and money.
Reduce Scrap
Diagnose issues correctly and decrease incorrect parts delivery. Train and guide technicians in more effective machinery repair and maintenance.
Maximize Productivity
Fill skill gaps, train less-experienced technicians, and connect them to experts. Minimize travel. Predict and solve issues before they occur.
Optimize Safety and Compliance
Increase safety by using remote guidance to maintain social distancing. Comply with maintenance regulations through more efficient machinery upkeep.
Manufacturing Use Cases
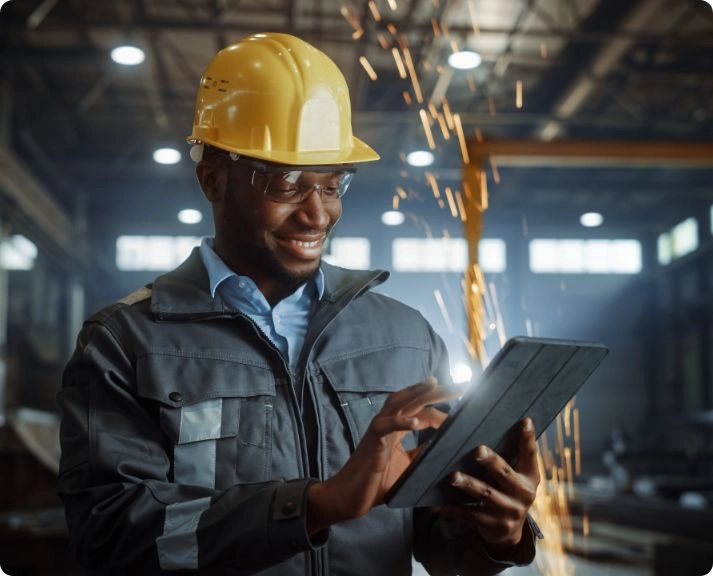
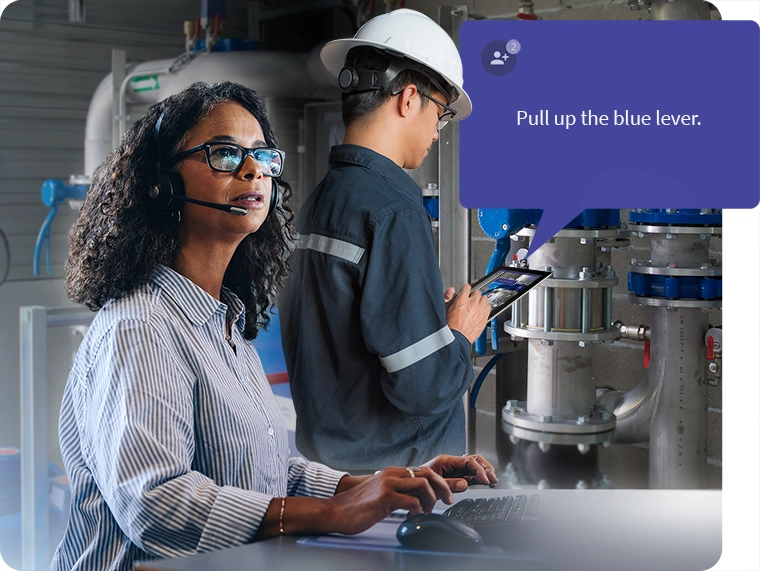
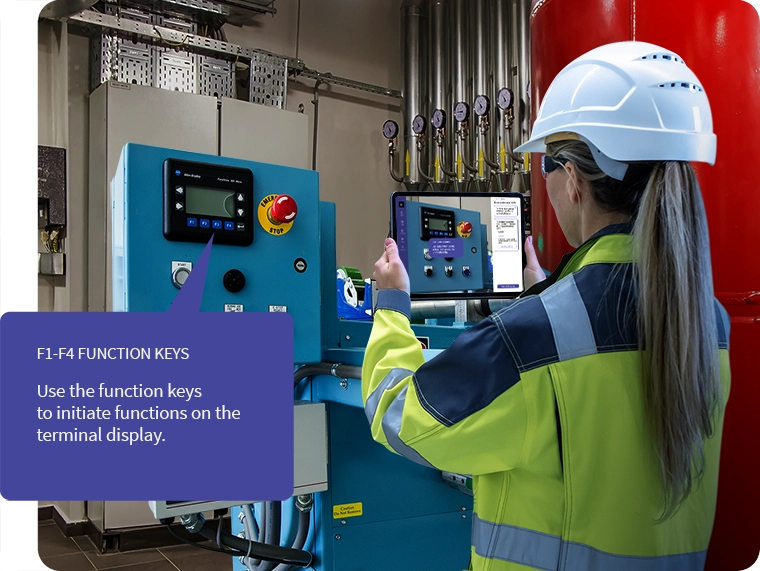
Production and Manufacturing Operations
OEM Product Support
Heavy and Complex Machine Service
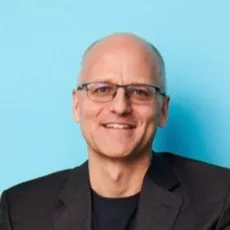
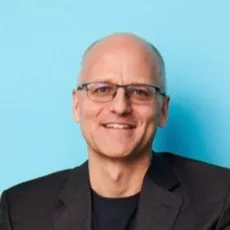
“Service teams today are challenged with solving problems in increasingly complex situations, especially in light of COVID-19. They want to increase efficiency, reduce operational costs, and improve customer outcomes—all while ensuring employee safety. Together with CareAR, ServiceNow is delivering digital experiences that empower service teams to better solve problems remotely so work can be completed efficiently and safely.”
Michael Ramsey,
VP of Product Management, ServiceNow